This article is contributed by Varinderjit Singh, General Manager at Lenovo Malaysia.
Those of us in the manufacturing industry have already come to terms with a difficult truth: manufacturing output is set to shrink by 3.2% this year. Stringent regulations and decreased consumer demand are proving very trying in a recessionary environment.
And many manufacturers still find themselves short-staffed. They are tasked with doing more with less. Upping output without the talent and financial resources they relied on in the past.
I see only one way forward: doing whatever we possibly can to create a streamlined working environment. Organizations that get hung up on what they don’t have will fall behind. Smart organizations think laterally. They understand that they have the means to effect change on their environments. And that seemingly small changes quickly add up.
Creating a streamlined, productive environment is the way forward. Increasing operational efficiency has never been as crucial as it is at this moment in time. Organizations that take action to create this kind of environment now will reap the rewards and come out stronger.
The three building blocks of an efficient environment
1. Making the most of your assets with IT and OT convergence
As a reminder, IT is Information Technology, tools that process data. OT is Operational Technology, tools for managing physical assets. IIoT (Industrial Internet of Things) technology can bring IT and OT together. With IIoT tools like smart sensors, digital twins, and machine learning, physical assets come to life in the IT space. When leadership can see crucial data and insights on how machines are doing, they can ensure that they make the most of them. A great example of a product that can assist with making the most of your assets through IT convergence is the ThinkPad® X1 Carbon Gen 11, powered by Intel® Core™ i5-1335U processor (13th Gen), built for what IT needs and users want.
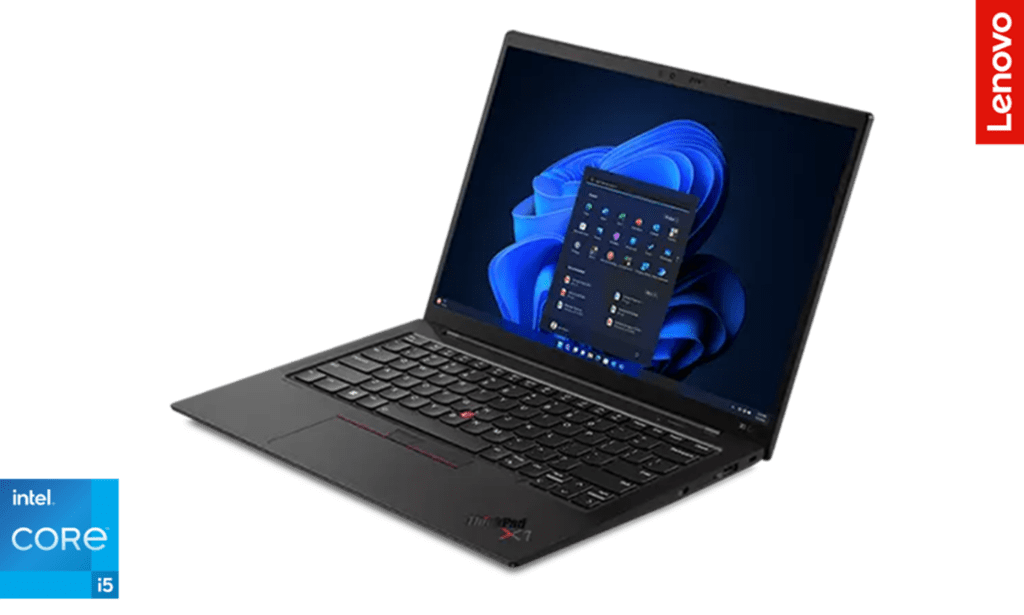
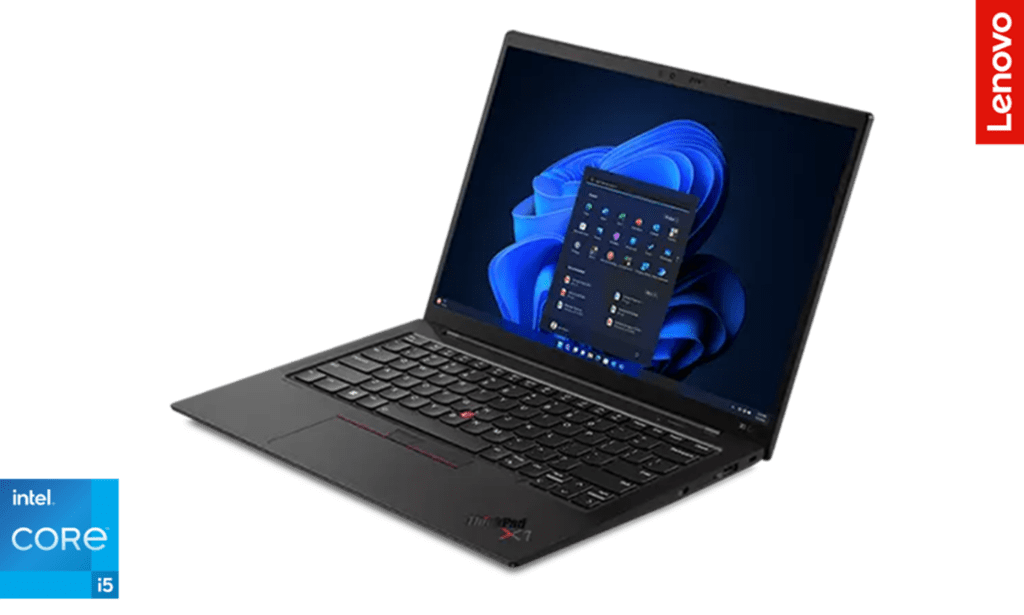
Utility consumption monitoring is a great example of the benefits of converged IT and OT. Electricity, water, and gas make up a significant part of any manufacturer’s budget. Sensors on the factory floor can detect when a process consumes more power than necessary. This data is then acted on in real time – and the process is automatically adjusted until it’s optimal. For example, temperature and water use can automatically be controlled to create an environment that supports efficient energy use. Where equipment needs to be warmer to operate, they can automatically be switched on when the time’s exactly right – eliminating the wastage that comes with guessing the wrong timing. Sensors that detect compressed-air leaks allows leadership to act before more energy goes to waste.
The cumulative savings tend to make a profound difference to utility bills. Even better: IIoT helps manufacturers get closer to their ESG goals and safeguard the environment.
2. Staying a step ahead with predictive maintenance
The technological advances in predictive maintenance are some of the most exciting I’ve seen in my career. Instead of waiting for machines to break down, we can now proactively prevent them from reaching a state of disrepair. There’s now no reason for manufacturers to be wrong-footed by ‘cranky’ or ‘moody’ machinery.
In order to reap the benefits of predictive maintenance, manufacturers need to have the right solutions in place. High-quality sensors, reliable and fast connectivity, and servers that can process asset data and allow it to be analyzed, fast.
Naturally, I’m a big advocate of Lenovo’s ThinkEdge servers, powered by Intel® and enabled by AI. These servers have the processing power required to make quick work of asset data. They are rugged and sturdy and can withstand extreme temperatures, dust, and vibration. My clients store these servers on the floor, close to where data is generated. This reduces latency between data collection and a resulting insight – allowing leadership to act fast when an AI alerts them of a potential issue or a worrisome trend.
3. Keep quality high with virtual inspection
In manufacturing, high-quality products are what we live for, and inspection is a crucial process for any manufacturer. More and more, I’m seeing manual quality assurance become a thing of the past.
Continuous, virtual inspection means that manufacturers can track every process, part, and final product. If a quality issue arises on the floor, IIoT technology means that a real-time notification will trigger necessary corrective actions for related processes or down-the-line tasks – including dynamically adjusting product runs.
This kind of intelligent inspection leads to time and money saved. Fixing potential issues before they lead to defective products is obviously much less costly than tossing out goods that are not up to standard. But it’s more than that: a smart factory floor with integrated IT and OT means that AI is continuously learning to improve and streamline processes. This allows manufacturers to create products they can be proud of, keeping their customer experiences high while boosting their productivity. It’s a win-win.